
物流倉庫内のモノの移動を自動化し、省人化と業務負荷軽減を実現(アルペン)
【Vol.4】アルペン 執行役員 物流本部長 兼 サプライチェーン・ロジスティクス部長 濱中 龍一(はまなか りゅういち)氏
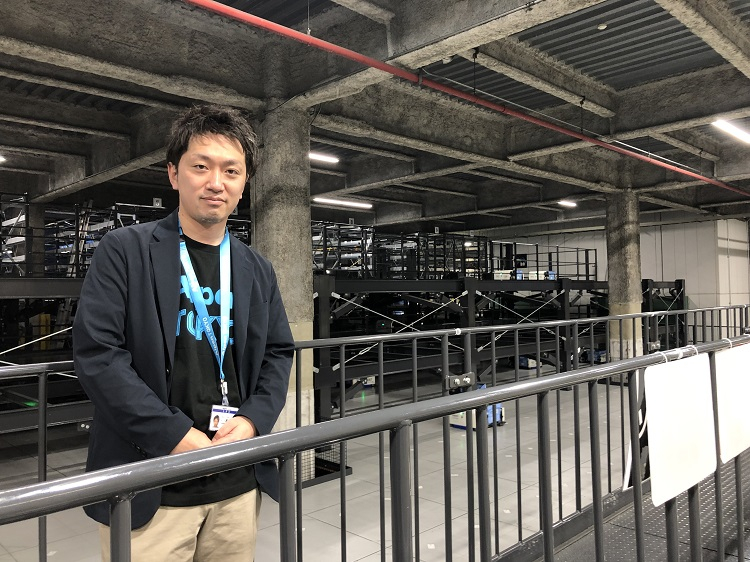
労働集約型の業務の1つである物流において、ロボットなどの活用による省人化の取り組みが進められている。テクノロジーの導入は、新たな働き手に来てもらうための労働環境の改善にもつながり、リードタイムの短縮といった競争力強化にも効果が期待できる。国内初のALPHABOT導入など、積極的にテクノロジーを取り入れているアルペン 執行役員 物流本部長 兼 サプライチェーン・ロジスティクス部長の濱中龍一氏に、ロボット導入の効果や課題について聞いた。
倉庫作業員の確保が困難に、働き方の抜本的な見直しを模索
スポーツ用品販売チェーンのアルペンでは戦略的に物流DXを進めている。背景にあるのは働き手不足だ。倉庫内作業員の雇用の確保が難しくなり、賃金上昇が物流コストを圧迫しつつある。濱中氏は「アルバイトの応募が確実に減少しており、派遣スタッフも依頼した人数を下回るようになってきました。年々、雇用が厳しくなっているのを肌で感じています」と話す。
物流業界における人手不足の要因としては、労働力人口の減少に加え、業種自体の不人気もある。重いものを運ぶ必要があることなどから、若い世代が集まりにくく、労働者の高齢化が進む。
「当社でもテントやトレーニングマシンなど大型の商品を扱っており、これらの積み下ろしは相当な力仕事になります。また、倉庫内は夏は暑く、冬は寒い。大型シーリングファンを設置するなど、アメニティ面からも労働環境の改善は進めていますが、倉庫全体にエアコンを完備するには数千万円単位の投資となるため、なかなか難しいところです」(濱中氏)
一方で、物流の効率化は成長戦略としても避けては通れないものになりつつある。ECの需要増に伴って多品種化、小ロット化が進んでおり、作業の手間や工数が増えてきた。また、翌日配送や当日配送が消費者にとって当たり前になったことから、物流の遅延は販売機会の損失にもつながる。
「ECの配送においては、配送リードタイムが顧客満足度を大きく左右します。今や物流の効率化は人手不足対策のみならず、事業成長にとっても欠かせないものとなっています」(濱中氏)
倉庫で自動化しやすいのは「モノの移動」に関わるプロセス
同社の物流拠点は関東と中部に計6カ所。関東は店舗向けの物流センターとEC向けの東日本フルフィルメントセンターの2つ、中部は小物、大物、ウエア、シューズというアイテム別に4つの拠点が置かれている。物流拠点で働くスタッフは、倉庫の管理運営を行う社員が50名、倉庫内作業に従事するアルバイトや派遣スタッフが1000名以上に及ぶ。
倉庫内作業のプロセスは以下のようになる。
①コンテナやトラックからの商品の荷下ろし
②商品の検品
③倉庫内の棚へ商品を格納
④配送する商品のピッキング
⑤配送先ごとの商品の仕分け
⑥商品の梱包・封函
⑦配送エリアごとの商品の仕分け
⑧トラックへの商品の積み込み
①~③が入庫に関わる作業で、④~⑧が出庫に関わる作業。作業比率はおおよそ入庫3:出庫7という割合になっている。
こうした業務プロセスの中で同社が自動化したのは、倉庫内での荷物の搬送に関わる部分だ。例えば、棚入れ作業では人が台車を押したり、フォークリフトを運転しながら商品を運んでいるほか、ピッキングした商品は人が歩いて梱包場所まで持ってきている。「運ぶ」という単純な作業であれば、ロボットの自動走行やシャトルの活用によって自動化しやすい。
逆に自動化が難しいのはトラックからの荷下ろしやトラックへの積み込み、棚から商品を取り出すピッキングといった作業だ。商品の形状によって掴み方が複雑になるため、人の手の繊細さが必要だという。
「商品の形状をAI分析し、大きさ、重量、壊れやすさを把握しうまく掴むことを可能にする技術はある。ただし、そのようなロボットの導入コストを考えると、投資効果に見合わないのが現状です」(濱中氏)
格納時やピッキング時のモノの移動を自動化し、40~60%の省人化に成功
実際の自動化事例を見ていこう。
EC専用倉庫である東日本フルフィルメントセンターにGTP型(※)の棚搬送ロボットを56台導入したのは2018年3月。ビジネス成長に合わせて段階的に拡張しながら、現在は、約7000坪のエリアを216台のロボットが動き、商品が入った棚を作業員が待機する作業台のところまで自動で運んでいる。作業員は目の前に来た棚から手作業でピッキングを行い、梱包を行う。従来は作業員が広い倉庫内を探し歩いて商品のピッキングを行っていたが、該当商品の入った棚を作業台の前まで自動搬送することで探し歩く手間を省いた形だ。
(※)GTP型 GTPはGoods To Personの略称で、物流センターにおいて貨物をピッキングする作業者の場所や、棚入れする場所まで荷物を運んでくるタイプの物流ロボットを指す。
棚搬送ロボット導入後は作業工数が従来の4分の1になり、40%の省人化効果が生まれている。作業員がピッキングする際の通路だったスペースにも棚を置けるようになり、倉庫の保管能力も2倍になったという。また、作業員の業務負荷が軽減されたことから、募集をかけると人が集まりやすくなった。直接雇用するアルバイトの割合は従来、全従業員数の3割程度だったが、ロボット導入後には8割にまで増えたという。力仕事が減ったこともあり、半数程度が女性作業員になっている。
小物を扱う小牧ディストリビューションセンター(DC)では、2021年11月から日本初となる3Dロボット倉庫システム「ALPHABOT」が稼働している。このシステムでは、検品を終えた商品を入庫ステーションにセットすると搬送ロボットが自動で保管棚に格納。出庫の際には搬送ロボットが棚から商品ケースを取り出し、ピッキングステーションまで運ぶ。ピッキングステーションでは作業員がケースから該当商品をピッキングし、梱包を行う。これによって格納およびピッキング時の作業員の移動がなくなり、作業工数は従来の5分の2に減少、60%の省人化を達成した。また、搬送ロボットは棚に沿った立体的な移動も可能なため、垂直方向のスペースを活用した高密度保管ができるようになった。こうした自動化により、倉庫の出庫能力を大きく上げたことで、繁忙期以外の夜勤は不要になったという。また、東日本フルフィルメントセンター同様に、作業軽減がされたことで、人が集まりやすくなった。
2024年からはウエア、シューズを扱う2拠点を統合した4万3000平方メートルの大型倉庫を稼働する予定だ。この倉庫ではシャトル型自動倉庫システムとクロスベルトソーターを組み合わせ、倉庫内の商品の移動をより効率化する。それによって入庫から出庫までの全体工数で60%の省人化が可能になるという。
大口DC シームレスなマテリアルハンドリングシステム 鳥瞰図
継続的な改善とテクノロジーを使いこなす人材の育成が重要
濱中氏によれば、棚の搬送ロボットもALPHABOTシステムも、導入当初は作業効率が上がらなかったという。搬送ロボットの導入当初は、「自動で棚を運べるから」と、棚の保管密度を上げたため、ピッキング時に棚から商品を探す手間が増えた。「棚に保管するアイテム数を絞る」「ピックの操作画面に商品画像を表示する」「作業者の習熟度に応じてロボットの制御をする」といった試行錯誤を繰り返し、効率性を高めてきたという。
「『機械を入れれば省人化は達成』と思っていましたが、そう単純な話ではありませんでした。動かし方次第では逆に効率が落ちてしまう。各装置の特性を理解し、機械に合わせた運用を構築すること、さらに継続的にPDCAを回していく努力が必要。現在も毎週各倉庫の生産性を分析し、ベンダーとの会合を毎月設けて改善策を話し合っています」(濱中氏)
こうした物流DXの取り組みの中で、倉庫を管理する側の社員に求められるスキルも変わってきている。各種データを分析するアナリスト的な業務や、ロボットの効果を最大化するためのプロセスエンジニアリング的な業務が今後は必要になってくると濱中氏は言う。
「WMS(倉庫管理システム)に様々なデータが蓄積されることで、業務プロセスの改善やマーケティングなどに活用できるようにもなります。現在は各倉庫から1~2名の社員を選抜し、データの扱い方などについて教育しているところです。テクノロジーの活用に積極的な社員を管理職やリーダー職に引き上げることで、競争力のある物流体制を築いていきたい」(濱中氏)
2030~2040年頃には完全無人の倉庫も現れるが、それらは資金力のあるごく一部の企業に限られるだろう、と濱中氏は予想する。同社がテクノロジーの導入にあたって検討の対象とするのは10年未満で投資回収できると見込んだものに限られるという。投資回収までに10年以上かかるようなものになると、それまでにまったく新しい技術が出てきたり、事業環境が変化したりする可能性もあるからだ。
「ただし、ロボットの普及には事業者が一定のリスクを許容したうえで、導入に踏み切ることも大切でしょう。導入実績のない技術などはリスクヘッジの観点から見送りがちですが、国内初導入だからこそ得られる価格面やサポート面でのメリットもある。当社としてはそういったメリットも判断材料にしながら、積極的に新しいチャレンジをしていきたいと考えています」(濱中氏)