成功の本質
第89回 ペーパーラボ/セイコーエプソン
水を使わずオフィスで紙を再生
機密保持と資源循環を両立
正式名称は「PaperLab A-8000」。オフィスのバックヤードなどに設置されることを想定している。
Photo=セイコーエプソン提供
「中に人が入っているのでは?」。使用済みの紙を原料にして小型マシンで新しい紙を生産する。セイコーエプソンが開発した世界初の乾式オフィス製紙機「PaperLab(ペーパーラボ)」のデモ機が披露されると、場内からそんな声があがった。2016年12月の販売開始のちょうど1年前、東京ビッグサイトで催された環境展示会でのことだ。
1年後にお披露目された本機は横幅2.8メートル、高さ1.8メートル、奥行き1.4メートルと軽ワゴン車を一回り小さくしたほどの大きさ。給紙台に使用済みの紙をセットすると、約3分で排紙口から1枚目の新しい紙が姿を現す。以降、約5秒に1枚のペースで生産されていく。名刺用紙などの厚みのある紙や着色された紙もつくれる。
オフィスでの使用済みの紙をリサイクルする場合、一般的に、回収紙を製紙施設で再生し、販売業者を通じてまた搬入される。このサイクルが1台の装置の中で約3分で行われるのだ。
「初めてお見せすると、みんなキョトンとした顔をされます。使用済みの紙がオフィスで再生できるなど、なかなか信じてもらえませんでした」
そう語るのは開発リーダーを務めた市川和弘・ペーパーラボ事業推進プロジェクト部長だ。エプソンは主力のインクジェットプリンター事業で国内トップの座を競う。そのエプソンがなぜ、オフィス製紙機を開発したのか。きっかけは、長野県松本市の事業所にいた市川にかかってきた1本の電話だった。
「それは諏訪の本社の技術開発本部の副本部長からで、社長の碓井(稔)の意向を伝えてきました。世の中全体の流れを見ると、プリンターから出された紙についても何か困りごとがあるはずで、エプソンとしてできることがあるのではないか、紙の再生も含めて考えてくれと」
当時、市川は「新規事業の種探し」を担当していた。しかし、紙の再生は既に製紙会社が手がけており、エプソンの事業ともかけ離れている。一瞬、聞き流そうとしたが、「ちょっと待てよ」と踏みとどまった。
「一度、紙について自分で納得できるまで理解してから結論を出そう。そう思って行動を起こしたのが始まりでした。2010年2月のことでした」(市川)
納得できるまで突き詰める。世界初の技術を生み出すことができたのは、そんな市川流の仕事の仕方と無縁ではない。ペーパーラボの開発も、原点の「紙を知る」ことからスタートした。その経緯をたどってみよう。
「紙の使用」へのためらいをなくす
業試験場、和紙工房などを訪ね、自分の目で確かめた。役所や企業のオフィスを回っては、紙がどのように使われ、どう処理されているか、観察し続けた。紙に関する「入り口から出口まで」、ひと通り理解すると、やがて紙にまつわる困りごとが浮かび上がってきた。
「プリンターから出される紙の大半は機密文書で、使用後は外部業者に依頼し、費用をかけて処理する。その処理方法にお客さまは満足していなかったのです」(市川)
機密文書はシュレッダーで裁断されるが、紙片をスキャナで一つひとつ読み取り、専用ソフトを使えば復元が可能だ。そこでより細かく裁断すると紙の繊維が寸断され、リサイクルには向かなくなる。溶解処理も第三者がかかわる点では情報漏洩の可能性を否定しきれない。つまり、セキュリティの担保と循環型社会への貢献が両立できていない部分があった。同時に、市川はオフィスを見て回りながら、ある特徴的な光景にも気づいた。
「普段はパソコンで仕事をしているのに、考えごとをするときは紙に書き込んでいるのです。創造的な仕事には紙が向いている。調べると、オフィスでの紙の需要は減っていませんでした。一方、ペーパーレス化が叫ばれ、紙の使用にはためらいもある。このためらいを取り払うことができれば、もっと紙を使ってもらえるのではないか。結局、開発のコンセプトはこうなりました。セキュリティを担保するため、オフィス内で、使用済みの紙を必要なとき、必要なだけ、必要な紙に再生する、と」(市川)
技術のヒントは日本伝統の和紙
ところが、ここで決定的な壁にぶつかる。従来、古紙の再生には大量の水を必要としてきた。再生は「繊維化→結合→成形」という工程を経る。古紙を水で溶解して繊維に戻す工程だけでなく、繊維の主成分セルロースの分子同士が結合する際にも水分子が橋渡しをする。しかし、給排水設備を使う装置にしてしまうと、オフィスでは設置場所が限られるうえ、水漏れした場合、他の電子機器に悪影響を及ぼす。設置場所を問わないようにするには、水を使わずに繊維化と結合を可能にする装置をつくらなければならない。それは、古代エジプトでパピルスが発明されて以来の紙の常識を根底からくつがえす試みであり、技術的なブレイクスルーが必要だった。
「切る」「破る」「つぶす」「する」......市川は紙を細かくする「動詞」を書き出すと、もう1人のメンバーと一緒に、水を使わず繊維化する実験を開始。「藁をもつかむ思い」で、すり鉢やミキサーまで使い、100通り以上も試行錯誤を重ねた。
市川和弘氏
セイコーエプソンペーパーラボ事業推進プロジェクト部長兼コア技術開発センター部長
Photo=勝尾 仁
打開策のヒントは日本古来の和紙に隠れていた。
「和紙を引きちぎると切れた部分に繊維が出てきます。それをほぐしていくと1本1本の繊維に分かれていく。この『ほぐす』という行為を手段に落とし込んでいけばいい。ここから先は詳しくはお話しできないのですが、ある種の機械的衝撃を紙に与えたところ、繊維のほぐれた部分がポンと現れたんです。『あっ、これだな』とキーになる技術が見えた。まさに日が差した瞬間です。考えた期間はそんなに長くありませんでしたが、四六時中考え抜く深い時間でした。開発1年目の2010年末のことでした」(市川)
市川は入社以来約30年間、時計、産業用ロボット、モーター用磁石、生産技術、レーザープリンター......と幅広い分野の仕事に携わってきた。「今回の開発にいろいろな経験が非常に生きた」という。
「結合もそうです。レーザープリンターに使うトナー(インク)に関連した、材料を均一に分散させる技術を活用したら、『あっ、できた』と思えた瞬間があった。ここから『ペーパープラス』という独自の素材で結合させる技術が生まれました」(市川)
自分たちで稼ぎながら開発する
紙が繊維化した状態。形状も手触りも綿そっくりだ。
ドライファイバーテクノロジーでつくられた厚紙状のインク吸収体。同社のプリンターに組み込まれている。
ペーパーラボによってつくられた再生紙。サイズはA3かA4で、着色したり、密度や厚みをコントロールすることで名刺向きの紙にしたりもできる。
Photo=勝尾 仁
水を使わず紙を再生する技術は「ドライファイバーテクノロジー」と命名された。以降、実際の製品づくりへと移行。各部門からメンバーが集められた。ここで注目すべきは、「稼ぎながら開発する」方法がとられたことだ。
インクジェットプリンターには印刷時などに出る余分なインクを吸い取る吸収体が内蔵されている。従来は外から買っていたが、使用済みの紙を原料に、ドライファイバーテクノロジーを使って厚紙状のものをつくり出せれば内製が可能だ。市川はこれをプリンター事業部に提案した。「過去の反省を活かした」という。
「新製品の開発にはかなりの時間を要します。レーザープリンターは10年以上でした。その間、お金がかかります。ならば開発途上でも会社に貢献したい。われわれがつくったほうが性能もコスト面も優れている。稼ぎながら開発を進める過程で『見えていない課題』も判明し、技術を熟成させることもできるだろうと考えました」実際、吸収体製造装置の開発を始めると、さまざまな課題が見えてきた。設計を託された藤田恵生・ペーパーラボ事業推進プロジェクト課長が話す。
「装置内でフワフワになった紙の繊維(上の左の写真参照)を形を変化させながら次の工程に送る技術を確立するのが大変でした。生産技術はじめ、各部門から参加したエンジニアがアイデアを持ち寄り、最後には解決することができました」
完成した吸収体の製造装置は工場で使用されるものだから、かなり大きかった。プリンター事業部に無事納品され、「稼ぐ」ことに貢献する。
そこから装置のダウンサイジング化などを進め、ついにペーパーラボのデモ機が完成。2015年12月、冒頭で述べた環境展示会での技術発表につながる。
「手のひら」に乗せて考える
紙の成形に必要な結合素材、ペーパープラス。ホワイト、イエロー、マゼンタ、シアンがあり、着色もできる。
Photo=セイコーエプソン提供
ペーパーラボの製紙法を改めてなぞってみよう。使用済みの紙は機械的衝撃により繊維化し、情報も完全に抹消される。次いで色が付着していた部分が除去された後、ペーパープラスが混合されて結合しシート状になる。ここで着色も可能だ。加圧して成形し厚さを調整、規格サイズにカットする。ランニングコストはA4サイズ1枚あたり0.45円と新品価格とほぼ同等だ。
デモ機は大反響を呼び、1時間ごとの実演は毎回満員。メディアの取材も殺到した。その結果、装置は1台2000万円台ながら、15の自治体、企業から導入の計画や検討の申し出が寄せられ、2016年12月の販売開始を迎えた。エプソンではそれらの自治体、企業を「プレミアムパートナー」と呼び、ペーパーラボの使用データや新たな活用法のアイデアを提供してもらい、商品価値の向上につなげていくという。
「紙の未来を変える」とのキャッチコピーどおり、製紙の歴史を塗り替えるほどの新しい技術をなぜ生み出すことができたのか。それは、「手段からではなく、目的から入ったから」と市川は言う。「今ある手段から入ると発想がそこで切れてしまいます。目的から入れば手段はいくらでも考えられる。今回も『できない』とは一度も思わず、『できる』ためにはどうするかを考え続けました」
藤田恵生氏
セイコーエプソンペーパーラボ事業推進プロジェクト課長
Photo=勝尾 仁
これはレーザープリンターの開発時の話だが、当初トナーを外部調達していたため、トナーに課題が生じても、根本的な解決ができなかった。市川は事業部から研究開発部門へ異動を願い出て、トナーの研究を根本からやり直した。自分で納得するまで理解することを「手のひらに乗せる」と表現し、「何が本質なのかを把握できる」と話す。「紙を知る」ことから始めたのもそのためだ。
好きな映画は「バック・トゥ・ザ・フューチャーPARTⅡ」。主人公の前に未来からタイムマシンのデロリアンが現れ、30年後の2015年にタイムトラベルする。SFで描かれる未来のツールを見てその発想を学ぶため、年2回は見直すという。物事の本質をつかみ、既存の概念に縛られなければ、自由に発想できる。近未来、家庭で古紙を再生する時代も来るかもしれない。(文中敬称略)
Text=勝見 明
日本の強みは組織的イノベーション
起点はリーダーの「跳ぶ推論」にある
一橋大学名誉教授
ペーパーラボのイノベーションから何を学ぶべきか。1つは開発リーダーの思考と行動に表れた、イノベーションを生む「知の作法」だ。
循環型社会への貢献が求められるなか、紙の使用はためらいをともなう。市川氏はためらいからの解放とセキュリティ問題の解決に向け、第三者が介在しないオフィスで「使用済みの紙を必要なとき、必要なだけ、必要な紙に再生する」というコンセプトを描いた。刮目すべきは、ここで「水を使わずに紙を再生する」という「跳ぶ推論(アブダクション)」を導き出したことだ。
市川氏はなぜアブダクションができたのか。それは紙に対する本質直観による。製紙業は水との関係が深く、静岡や愛媛など製紙業が盛んな土地は豊かな湧き水で知られ、製紙業者なら、紙の本質は「水」であるという固定概念にとらわれたはずだ。一方、市川氏は紙の本質は水以上に「繊維化と結合」にあるととらえた。それは精密機器の技術者として幅広い分野で蓄積された経験知による。それらが総合され、「水を使わない再生」という跳ぶ推論が生成された。
その実現に向けた試行錯誤のなかで、あるとき、技術の軸が見える瞬間が訪れる。「これだな」とひらめく「アハ!体験(A-ha! Experience)」である。市川氏はほぐれた紙の繊維から、目指す技術の軸を見出した。イノベーションにとって、豊富な経験知に基づく試行錯誤の大切さを改めて実感する。
この事例からもう1つ学ぶべきは、組織的なイノベーションの起こし方だ。トップの課題提起に触発されたミドルリーダーが幅広い部門のメンバーを巻き込み、仮説を具現化していく。さらに、自分たちの成果物について他の事業部と社内取引を行い、稼ぎながら経営に貢献し、技術を熟成させる。ミドルが組織の縦横の結節点に立ち、組織力を最大限活用する進め方は「賢い開発」の1つの範といえよう。
アメリカなどのIT企業では一部の天才がイノベーションを起こし、それを論理的思考に長けた「頭のいい人材」が支える構図だ。一方、日本のメーカーでは、身体性をともなった多様な経験知が蓄積され、ミドルリーダーによる跳ぶ推論をもとに知が総動員され、イノベーションに至る。これが日本の強みであることを再認識すべきだ。
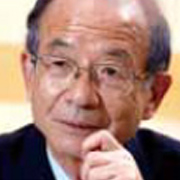
野中郁次郎氏
一橋大学名誉教授
Nonaka Ikujiro 1935年生まれ。早稲田大学政治経済学部卒業。カリフォルニア大学経営大学院博士課程修了。知識創造理論の提唱者でありナレッジマネジメントの世界的権威。2008年米経済紙による「最も影響力のあるビジネス思想家トップ20」にアジアから唯一選出された。『失敗の本質』『知識創造企業』など著書多数。